Aço de Damasco
O aço de Damasco era o aço forjado que compreendia as lâminas de espadas forjadas no Oriente Médio a partir de lingotes aço sérico (aço de wootz)[1] que eram importados da Índia e do Sri Lanka. Essas espadas são caracterizadas por padrões distintos de faixas e manchas que lembram o fluxo de água. Essas lâminas eram reputadas como resistentes, resistentes a estilhaços e capazes de serem afiadas a uma borda afiada e resistente.[2]
O aço deve o seu nome a Damasco, a capital da Síria e uma das maiores cidades do antigo Levante. Pode referir-se a espadas feitas ou vendidas diretamente em Damasco, ou pode apenas se referir ao aspecto dos padrões típicos, em comparação com os tecidos de Damasco (que são nomeados após Damasco).[3][4]
O método original de produzir ácido sérico não é conhecido. Modernas tentativas de duplicar o metal não foram totalmente bem sucedidas devido a diferenças nas matérias-primas e técnicas de fabricação. Várias pessoas nos tempos modernos afirmaram ter redescoberto os métodos pelos quais o aço original de Damasco foi produzido.[5][6][7]
A reputação e a história do aço de Damasco deram origem a muitas lendas, como a habilidade de cortar um cano de fuzil ou cortar um fio de cabelo caindo sobre a lâmina.[8] Uma equipe de pesquisa na Alemanha publicou um relatório em 2006 revelando nanofios e nanotubos de carbono em uma lâmina forjada a partir de aço de Damasco.[9][10][11] Embora muitos tipos de aço moderno superem as antigas ligas de Damasco, reações químicas no processo de produção tornaram as pás extraordinárias para a época, já que o aço de Damasco era superplástico e muito duro ao mesmo tempo. Durante o processo de fundição para obter lingotes de aço sérico, sabe-se que a biomassa lenhosa e as folhas foram usadas como aditivos de cementação, juntamente com certos tipos específicos de ferro, ricos em elementos microligantes. Esses lingotes seriam então forjados e trabalhados em lâminas de aço de Damasco. Pesquisas mostram agora que os nanotubos de carbono podem ser derivados de fibras vegetais,[12] sugerindo como os nanotubos foram formados no aço. Alguns especialistas esperam descobrir esses nanotubos em mais relíquias à medida que são analisados mais de perto.[10]
História
[editar | editar código-fonte]
As lâminas de Damasco foram fabricadas no Oriente Médio a partir de lingotes de aço sérico importados da Índia,[1] bem como do Sri Lanka.[13] Os árabes introduziram o aço sérico em Damasco, onde a indústria de armas prosperou.[14] Do século III ao século XVII, lingotes de aço eram enviados para o Oriente Médio pela Índia.[15]
Perda da técnica
[editar | editar código-fonte]A produção dessas espadas padronizadas diminuiu gradualmente, cessando por volta de 1750, e o processo foi perdido para os ferreiros. Várias teorias modernas se aventuraram a explicar esse declínio, incluindo a quebra de rotas de comércio para suprir os metais necessários, a falta de impurezas nos metais, a possível perda de conhecimento sobre as técnicas de fabricação por meio de sigilo e falta de transmissão, supressão da indústria na Índia pelo Raj britânico,[16] ou uma combinação de todos os acima.[5][6][17]
O aço sérico original era importado da Índia para Damasco, onde os cuteleiros do Oriente Médio os forjaram em espadas.[5][6] Devido à distância do comércio para este aço, uma interrupção suficientemente longa das rotas comerciais poderia ter terminado a produção de aço de Damasco e, eventualmente, levou à perda da técnica na Índia. Além disso, a necessidade de impurezas-chave de tungstênio ou vanádio dentro dos materiais necessários para a produção do aço pode estar ausente se este material foi adquirido de diferentes regiões de produção ou fundido a partir de minérios sem esses elementos-chave.[5] A técnica para o ciclo térmico controlado após o forjamento inicial a uma temperatura específica também poderia ter sido perdida, evitando assim que ocorra o padrão damasco final no aço.[5][6]
A descoberta de nanotubos de carbono na composição do aço de Damasco sustenta essa hipótese, uma vez que a precipitação de nanotubos de carbono provavelmente resultou de um processo específico que pode ser difícil de replicar caso a técnica de produção ou as matérias-primas utilizadas sejam significativamente alteradas.[17]
Reprodução
[editar | editar código-fonte]Recriar o aço de Damasco é um subcampo da arqueologia experimental. Muitos tentaram descobrir ou fazer engenharia reversa do processo pelo qual ela foi feita.[carece de fontes]
Moran: soldagem de tarugos
[editar | editar código-fonte]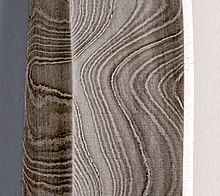
Desde a conhecida técnica de soldagem de padrões ; a soldagem de forja de uma lâmina de várias peças diferentes produziu padrões de superfície semelhantes aos encontrados em lâminas de Damasco, alguns ferreiros modernos foram erroneamente levados a acreditar que as lâminas originais de Damasco foram feitas usando essa técnica. No entanto, hoje, a diferença entre o aço sérico e a padrão do desenho é totalmente documentada e bem compreendida.[18][19][20] O padrão do desenho do aço tem sido chamado de "aço de Damasco" desde 1973, quando o ferreiro William F. Moran revelou suas "facas de Damasco" no Knifemakers 'Guild Show.[21][22]
Este "Damasco Moderno" é feito de vários tipos de lâminas de aço e ferro soldadas para formar um tarugo (produto semiacabado), atualmente o termo "Damasco" (embora tecnicamente incorreto) é amplamente aceito para descrever o padrão moderno de lâminas de aço soldado no comércio.[23] Os padrões variam dependendo de como o ferreiro trabalha o tarugo. O tarugo é retirado e dobrado até que o número desejado de camadas seja formado.[22] Para obter uma classificação de Mestre ferreiro com a American Bladesmith Society que Moran fundou, o ferreiro deve forjar uma lâmina de Damasco com um mínimo de 300 camadas.[24]
Verhoeven e Pendray: cadinho
[editar | editar código-fonte]JD Verhoeven e AH Pendray publicaram um artigo sobre suas tentativas de reproduzir as características elementares, estruturais e visuais do aço de Damasco.[5] Eles começaram com um bolo de aço que combinava com as propriedades do original aço sérico da Índia, que também combinava com uma série de espadas Damasco originais que Verhoeven e Pendray tinham acesso. O aço sérico estava em um estado suave e recozido, com uma estrutura de grãos e contas de carboneto de ferro puro, que resultavam de seu estado hipereutetóide. Verhoeven e Pendray já haviam determinado que os grãos na superfície do aço eram grãos de carboneto de ferro. O seu objetivo era reproduzir os padrões de carboneto de ferro que viam nas lâminas de Damasco dos grãos no aço sérico.[carece de fontes]
Embora esse material pudesse ser trabalhado a baixas temperaturas para produzir o padrão estriado de Damasceno de faixas de ferrite e cementita misturadas de maneira idêntica ao padrão do aço de Damasco, qualquer tratamento térmico suficiente para dissolver os carbonetos destruiria permanentemente o padrão. No entanto, Verhoeven e Pendray descobriram que em amostras de aço verdadeiro de Damasco, o padrão Damasceno poderia ser recuperado pelo envelhecimento a uma temperatura moderada. Eles descobriram que certos elementos formadores de carboneto, um dos quais era o vanádio, não se dispersaram até que o aço atingisse temperaturas mais altas do que as necessárias para dissolver os carbonetos. Portanto, um tratamento de alta temperatura poderia remover a evidência visual de padronização associada a carbonetos, mas não removeu o padrão subjacente dos elementos formadores de carboneto; um tratamento térmico subseqüente a baixa temperatura, a uma temperatura na qual os carbonetos eram novamente estáveis, poderia recuperar a estrutura pela ligação do carbono por esses elementos.[carece de fontes]
Anosov, Wadsworth e Sherby: bulat
[editar | editar código-fonte]Na Rússia, as crônicas registram o uso de um material conhecido como aço bulat para fabricar armas de alto valor, incluindo espadas, facas e machados. O czar Miguel da Rússia supostamente tinha um capacete feito para ele em 1621. A origem exata ou o processo de fabricação do bulat é desconhecido, mas provavelmente foi importado para a Rússia através da Pérsia e do Turquestão e deveria ser semelhante e possivelmente era o mesmo processo do aço de Damasco. Pavel Petrovich Anosov fez várias tentativas de reproduzir o processo em meados do século XIX. Wadsworth e Sherby também pesquisaram[6] a reprodução do aço bulat e publicaram seus resultados em 1980.

Pesquisa adicional
[editar | editar código-fonte]Uma equipe de pesquisadores da Universidade Técnica de Dresden, que usou raios X e microscopia eletrônica para examinar o aço de Damasco, descobriu a presença de nanofios de cementita[25] e nanotubos de carbono.[9] Peter Paufler, membro da equipe de Dresden, diz que essas nanoestruturas são resultado do processo de forjamento.[10][26]
Sanderson propõe que o processo de forjar e recozir conta para a formação das estruturas em nanoescala.[26]
No fabrico de armas
[editar | editar código-fonte]Antes do início do século XX todos os canos de espingarda foram forjados aquecendo tiras estreitas de ferro e aço e moldando-as em torno de um mandril. Este processo foi referido como "laminação" ou "Damasco".[27][28] Esses tipos de canos de armas ganhavam uma reputação pela sua fraqueza e nunca deveriam ser usados com pó moderno sem fumaça, ou qualquer tipo de explosivo moderadamente poderoso.[28] Por causa da semelhança com o aço de Damasco, os barris mais sofisticados eram feitos por fabricantes de armas belgas e britânicos.[27][28] Estes canos era feito o teste de prova e deviam ser usados com cargas de pressão leves.[27] Fabricantes de armas atuais fazem montagens de slides e pequenas peças, como gatilhos e dispositivos de segurança para pistolas Colt M1911 de aço sueco em pó, resultando em um efeito de dois tons redemoinho; estas peças são muitas vezes referidas como "Damasco inoxidável".[29]
Ver também
[editar | editar código-fonte]Referências
- ↑ a b Pacey, Arnold. Technology in World Civilization: A Thousand-year History. [S.l.: s.n.] ISBN 978-0-262-66072-3
- ↑ Figiel, Leo S. On Damascus Steel. [S.l.: s.n.] ISBN 978-0-9628711-0-8
- ↑ Goddard, Wayne. The Wonder of Knifemaking. [S.l.: s.n.] ISBN 978-0-87341-798-3
- ↑ Williams, Alan R. The knight and the blast furnace: a history of the metallurgy of armour in the Middle Ages & the early modern period. Col: History of warfare. 12. [S.l.: s.n.] ISBN 978-90-04-12498-1
- ↑ a b c d e f «The key role of impurities in ancient damascus steel blades». Journal of Metallurgy. 50. Bibcode:1998JOM....50i..58V. doi:10.1007/s11837-998-0419-y
- ↑ a b c d e «On the Bulat – Damascus Steel Revisited». Prog. Mater. Sci. 25. doi:10.1016/0079-6425(80)90014-6
- ↑ John Verhoeven: O mistério das espadas de aço de Damasco reveladas
- ↑ Becker, Otto Matthew. High-speed steel: the development, nature, treatment, and use of high-speed steels, together with some suggestions as to the problems involved in their use. [S.l.: s.n.]
- ↑ a b «Materials: Carbon nanotubes in an ancient Damascus sabre». Nature. 444. Bibcode:2006Natur.444..286R. PMID 17108950. doi:10.1038/444286a
- ↑ a b c «Legendary Swords' Sharpness, Strength From Nanotubes, Study Says», National Geographic News, 18 de novembro de 2006, arquivado do original em 4 de janeiro de 2007
- ↑ «Antique Nanotubes». New York Times
- ↑ «Carbon nanotubes produced from natural cellulosic materials». Journal of Nanoscience and Nanotechnology. 8. PMID 18572666. doi:10.1166/jnn.2008.235
- ↑ «An ancient wind powered iron smelting technology in Sri Lanka». Nature. 379. Bibcode:1996Natur.379...60J. doi:10.1038/379060a0
- ↑ Sharada Srinivasan; Srinivasa Ranganathan. India's Legendary Wootz Steel: An Advanced Material of the Ancient World. [S.l.: s.n.] OCLC 82439861
- ↑ Sinopoli, Carla M. The Political Economy of Craft Production: Crafting Empire in South India, c. 1350–1650. [S.l.: s.n.] ISBN 0-521-82613-6
- ↑ «The Book of the Sword». ISBN 1605204366
- ↑ a b «Carbon nanotubes: Saladin's secret weapon». Royal Society of Chemistry
- ↑ «A Sword of the Nydam Type from Ely Fields Farm, near Ely». Proceedings of the Cambridge Antiquarian Society. XLI. doi:10.5284/1034398
- ↑ «Pattern-Welding and Damascening of Sword-Blades—Part 1: Pattern-Welding». Studies in Conservation. 5. JSTOR 1505063. doi:10.2307/1505063
- ↑ «Pattern-Welding and Damascening of Sword-Blades—Part 2: The Damascene Process». Studies in Conservation. 5. JSTOR 1504953. doi:10.2307/1504953
- ↑ Lewis, Jack; Roger Combs. Gun digest book of knives. [S.l.: s.n.] ISBN 978-0-87349-129-7
- ↑ a b Kertzman, Joe. Art of the Knife. [S.l.: s.n.] ISBN 978-0-89689-470-9
- ↑ Loveless, Robert; Barney, Richard. How to Make Knives. [S.l.: s.n.] ISBN 0-695-80913-X
- ↑ «ABS Testing Rules and Guidelines for the Master Smith Rating» (PDF)
- ↑ «Nanowires in ancient Damascus steel». Journal of Alloys and Compounds. 372. ISSN 0925-8388. doi:10.1016/j.jallcom.2003.10.005
«Microstructure of a genuine Damascus sabre» (PDF). Crystal Research and Technology. 40. doi:10.1002/crat.200410456 - ↑ a b «Sharpest cut from nanotube sword». Nature. 444. doi:10.1038/news061113-11
- ↑ a b c Simpson, Layne. Shotguns & Shotgunning. [S.l.: s.n.] ISBN 978-0-87349-567-7
- ↑ a b c Matunas, Edward A. Do-It-Yourself Gun Repair. [S.l.: s.n.] ISBN 978-0-9722804-2-6
- ↑ «Damascus Knight .45». American Handgunner Magazine. 20
Ligações externas
[editar | editar código-fonte]- Nanotubos de carbono no aço damasco
- "Técnica Damascena no Metalúrgico"
- «The continuing study of damascus steel: Bars from the Alwar Armory». JOM. 56. Bibcode:2004JOM....56i..17V. doi:10.1007/s11837-004-0193-4
- «Pattern Formation in Wootz Damascus Steel Swords and Blades» (PDF). Indian Journal of History of Science. 42
- John Verhoeven: O mistério das espadas de aço de Damasco reveladas
- The Secrets of Wootz Damascus Steel (em inglês)